Brushes are often used for deburring of undefined geometries, such as cast workpieces. The brush acts as a flexible, abrasive element. Despite this property, the service life of the brush is often short when used for anything other than manual deburring, and the quality of the brush is irregular and therefore “not process-reliable”.
Brushes work perfectly within a defined process window, i.e. with a defined circumferential speed, feed and brush pressure. Inaccurate geometry, slight deviations in the robots’ paths of travel and brush wear cause the process parameters to change within the same workpiece, but also from workpiece to workpiece within the current series. These deviations lead to unstable processes, which, in combination with increased tool costs, often lead to a project stop compared to manual deburring. This results in even series-produced parts being deburred manually again.
Is there a solution to this problem?
Yes, the solution is tools with a radial or axial flexibility – depending on the application. This adjustable parameter makes it possible to compensate for deviations in component geometry. In addition, the wear of the brush is also compensated so that the brush always works in the ideal process window (pressure). This ensures flawless quality and a long service life. The compliant tool compensates for human touch during manual brushing.
This means that difficulties in automated deburring can be corrected using suitable flexible tools, combining them with the advantages of automation. The unmanned production time and the constant deburring results due to always the same motion sequences are just two of many possible application-specific advantages.
The overarching topics are: Increased productivity, lower production costs, improved occupational safety through the substitution of manual deburring and increased process reliability when brushing.
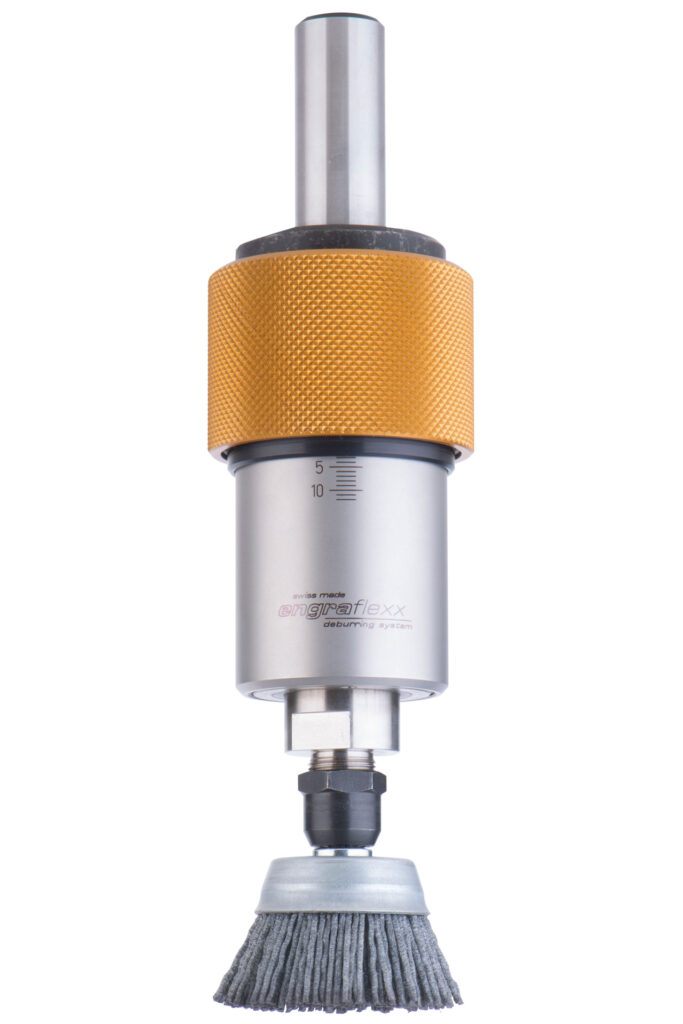
Stay up to date
With the gravostar e-mail newsletter you will regularly learn everything about process-integrated part marking or automated deburring.